A Tale of Two Water Towers: Difference between revisions
Line 29: | Line 29: | ||
File:WaterTower StrutJig.jpg|Start by welding a pair of A-frame support structures. Make a jig to hold the parts in place while welding. I used an old picnic table. Yes, I started a couple of small fires, but no real damage done. | File:WaterTower StrutJig.jpg|Start by welding a pair of A-frame support structures. Make a jig to hold the parts in place while welding. I used an old picnic table. Yes, I started a couple of small fires, but no real damage done. | ||
File:WaterTower WeldingJig.jpg|The welding jig can be very simple. Lay out the rebar on a flat wooden surface, then drive sheetrock screws into the wood as shown. | File:WaterTower WeldingJig.jpg|The welding jig can be very simple. Lay out the rebar on a flat wooden surface, then drive sheetrock screws into the wood as shown. | ||
File:Completed WaterTower Support.jpg|A completed A-frame support. Make two of these, then weld together as shown in the next photo. These were welded using a Lincoln "tomb stone" welder set at 90 amps, using #6013 1/8 inch rods. | File:Completed WaterTower Support.jpg|A completed A-frame support. Make two of these, then weld together as shown in the next photo. These were welded using a [https://www.google.com/search?q=Lincoln+tomb+stone+welder Lincoln "tomb stone" welder] set at 90 amps, using #6013 1/8 inch rods. | ||
File:WaterTower AFrame Assembly.jpg|Place the two completed A-Frame supports next to each other. Weld them together with 3/8 inch rebar cut to the appropriate lengths. Make sure the assembly is square before welding. | File:WaterTower AFrame Assembly.jpg|Place the two completed A-Frame supports next to each other. Weld them together with 3/8 inch rebar cut to the appropriate lengths. Make sure the assembly is square before welding. | ||
File:WaterTower WeldingTank On AFrame.jpg|Remove the handle and valve from the top of the freon tank. Sand down to the bare metal where the struts will be welded. The tank is welded upside-down onto the A-Frame support structure. The valve stem can be left in-tack in order to hold the one inch PVC pipe supply line. The tank wall is thin so use a low power setting (40 amps) and a small diameter stick (1/16 inch). Or, use a wire MIG welder. | File:WaterTower WeldingTank On AFrame.jpg|Remove the handle and valve from the top of the freon tank. Sand down to the bare metal where the struts will be welded. The tank is welded upside-down onto the A-Frame support structure. The valve stem can be left in-tack in order to hold the one inch PVC pipe supply line. The tank wall is thin so use a low power setting (40 amps) and a small diameter stick (1/16 inch). Or, use a wire MIG welder. |
Revision as of 11:48, 1 April 2015
31 March 2015
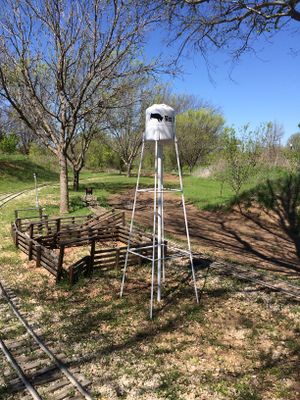
Every railroad is dependent upon it customers for survival. A healthy business climate in the areas of service will help guarantee success for the railroad. Therefore, it is incumbent upon the railroad to do all it can to spur growth in local business. Each siding, no matter how small, can add to the bottom line.
The managers of the Annetta Valley & Western Railroad considered how to encourage growth in the towns and sidings it services. Many issues were discussed, but one in particular "bubbled" to the top: water. It is recognized that every town and siding relies on a plentiful water supply for successful growth.
The most obvious example is the cattle exchange at West Fork. This siding has relied on water pumped from the ground by a windmill. The increase in the number of cattle shipped through the exchange has outgrown the amount of water that can be supplied by the windmill.
Another siding with increasing water needs is Shady Rest. Real estate magnates are promoting an industrial development next to the spur track. A water tower is required to provide the needs of the industries targeted for the development.
The AV&WRR board of directors approved loans for the construction of two 75,000 gallon water towers, one each for West Fork and Shady Rest. The railroad oversaw the construction and erection of the two towers. The project was completed on March 27, 2015.
Construction
I first saw this style water tower at Jack Haskin's Able Springs & North Texas Railroad. There are several such water towers at various towns and siding on his layout. They add a touch of realism, as most Texas towns boast at least one water tower.
Surprisingly, these model water towers are inexpensive to construct. The water tank is a steel, single use freon tank. You can obtain these from refrigeration repair companies. They are disposed of once empty. Another source is disposable helium tanks sold at Walmart and other retail outlets.
The legs and cross-braces are rebar, which is available at most building supply stores. The 1/2 inch rebar used for the legs is purchased in ten foot lengths. Simply cut them in half for the proper length of five feet.
A completed A-frame support. Make two of these, then weld together as shown in the next photo. These were welded using a Lincoln "tomb stone" welder set at 90 amps, using #6013 1/8 inch rods.
Remove the handle and valve from the top of the freon tank. Sand down to the bare metal where the struts will be welded. The tank is welded upside-down onto the A-Frame support structure. The valve stem can be left in-tack in order to hold the one inch PVC pipe supply line. The tank wall is thin so use a low power setting (40 amps) and a small diameter stick (1/16 inch). Or, use a wire MIG welder.
Most modern water towers are painted with the town name along with the town's logo. Simple logos were designed for each town to make the towers more interesting to visitors. The logos and lettering were designed using a free program named Inkscape. Paint masks were cut with a computer-driven vinyl cutter.
The second water tower was installed at the new industrial siding at Shady Rest on the Annetta Valley & Western Railroad.